PWL Oil & Gas Service Provider is the sole distributor for KSA and UAE of Villa macchine products. This Italian brand, well know on the market, plus the staff of Powerline technicians and engineers grant to our customer the suitable an reliable partner for the mechanical jobs in the pipeline projects.
PIPELINE EQUIPMENT
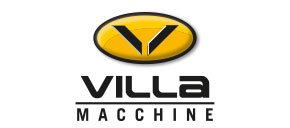
Paywelder
PAYWELDER MACH 1
Minipaywelder
Diesel engine 50 HP, low CO2 emission, rubber tracks, electric generator 25-30 KVA 400V-230V-48V
Inverter welding types: mig, mag, tic, special electrode; prearranged for polythylene welding
Telescopic illumination – Height 4 mt
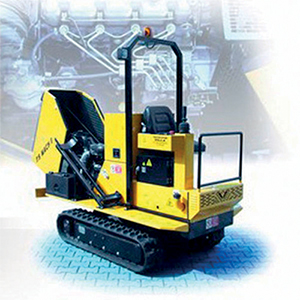
PAYWELDER MACH 2
Silened Eco Diesel engine 4C, 100 HP, generator – 80 kva cc, panel with available voltage 400V-230V-110V-48V
1 to 4 inverter welder carrier: mig, mag, tig, special electrode
15 bar air compressor with tank and safety accessories
4 unit hydraulic cylinder carrier with multi gas mixer
Hydraulic rotary crane with welding tent (with 48V smoke extractors) or telescopic arm and protective welding tent
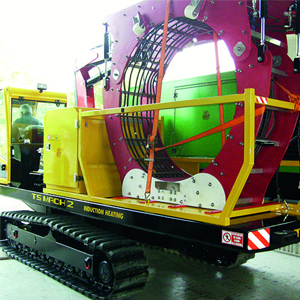
PAYWELDER MACH 3
Diesel engine 160 HP, generator – 180 kva, panel with available voltage 400V-230V-110V-48V
General switchboard, IP 66
1 to 4 inverter welder carrier mig, mag, tig, special electrode
15 bar air compressor with tank and safety accessories
6 unit hydraulic cylinder carrier with multi gas mixer
Telescopic hydraulic crane (7,6 m x 9,50) that operates at 340°, 30% slope arm full open
Welding tent ( with 48V smoke extractors)
Thermoventilated cabin – double speed
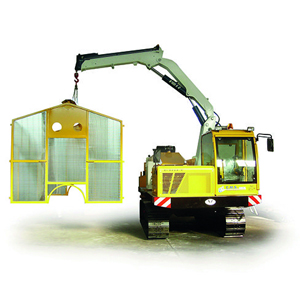
Automatic Welding Machine
TVS MACH 1
Highly flexible and operational, low operating costs, interchangeable and appropriate for different types of machining setups. Everything in the respect of the environment (low consumption, low pollution emission, low noise) Designed and developed around man, highly ergonomically, appropriate for town situations.
Diesel engine HP 50, low CO2 emission, rubber tracks, Electic generator 25-30 Kwa 400V-230V-48V, Inverter welding types: mig, mag, tig, special electrode. Prearranged for polythylene welding, Telescopic illumination – H mt. 4 – different types of watts, Closable tool container, Head lights and rotating beacon light,Operator seat with man on board safety system, Automatic reversing buzzer, protection Roll-bar, Mini fire extinguisher.
It can be equipped with: Hydraulic wire winch, Induction system with 400 A welding rod for pipes up until 14″/16″, Negative hydraulic brakes.
TVS MACH 2
Silenced Eco Diesel Engine 4C. HP 100 – Generator 80 Kwa cc – panel with available voltage 400V 230V 110V 48V, 1 to 4 inverter welding points: mig, mag, tig, special electrode prearranged for polyethylene welding. Air compressor at 15 bar vessel and safety accessories, 4 unit hydraulic cylinder carrier with multi-gas mixer, hydraulic rotary crane with welding tent (smoke extractors 48V included) or telescopic arm and protective welding tent, Thermoventilated cabin-double speed, Anatomically designed operator seat with man onboard safety system, Closable tool containers, High capacity fire extinguisher, General switchboard, protection level IP 66.
It can be equipped with: Hydraulic wire winch of different types of voltage, Sandblaster with high efficiency rotary air compressor, Different undercarriage tracks (farm steel or tell and rubber or rubber), Negative brakes, Illuminations of different types of watts, Induction Inverter-Preheating Coil/BandCoil2011 – Thermal treatment, GPS, Radio controller.
Available in custom made version:
Artic version -35°
Tropical version with air conditioning cabin and refrigerator on board
Amphibious version
Container transportation version
TVS MACH 3
Diesel Engine – HP 160 Generator – 180 Kwa – panel with available voltage 400V 230V 110V 48V, General switch board, protection level IP 66; 1 to 4 inverter welding points: mig, mag, tig, special electrode prearranged for polythylene welding. Air compressor at 15 bar vessel and safety accessories, 6 unit hydraulic cylinder carrier with multi gas mixer, Propane cylinder carrier, Telescopic hydraulic crane (mt.7,6×9,50) that operates at 340°, 30% slope arm full open, Welding tent (smoke extractors 48V included), Thermoventilated cabin-double speed, Anatomically designed operator seat with man on board safety system, Closable tool containers, High capacity fire extinguisher. It can be equipped with: Hydraulic wire winch of different types of voltage, Induction system – Inverter – Preheating Coil/Band Coil2011 – Thermal treatment, Automatic welding system, Sandblasting system, Different types of undercarriage tracks (farm steel or tell and rubber or rubber), Negative brakes, Illuminations of different types of watts, Radio controller.
Available in custom made version:
Artic version -35°
Tropical version with air conditioning cabin and refrigerator on board
Amphibious version
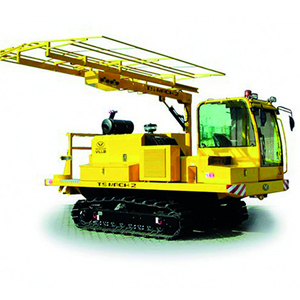
Automatic Welding System
ARIANNA
ARIANNA is an orbital automatic welding system created for all pipeline related applications including pipes with great wall thickness and connections.
ARIANNA is controlled by an industrial PLC that allows great application flexibility and to obtain the best welding in any work conditions and on any type of steel. The purpose of all this is to maximize the production, guaranteeing high quality standards of the welded joint.
ARIANNA is an open automatic system that allows interfacing with multiple devices, that is welders or external wire feeders, through analog or digital interfaces, and allows welding technicians and engineers to adapt the system, in the best way possible, to the position that needs to be performed.
Applications
Pipeline welding
Hot welding bend
Tie in welding
Prefabrication welding
System Components
Control Panel
Operator Panel
Remote Control
Welding heads
Welding power supply
Gas mixer
Power supply
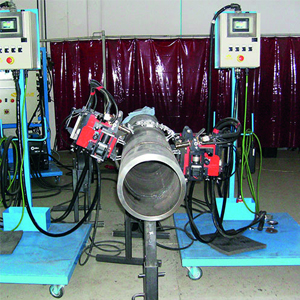
Induction System
The importance of fast, accurate and uniform heating as part of the pipeline welding specification has grown significantly. This has resulted from the increased use of heavy wall pipe and modern automatic and semi-automatic welding systems 0n/off shore pipeline.
The benefits of the induction heating system are:
Much faster temperature rise than gas or resistance heating
Variable control over temperature or time parameters
Accurate, uniform heating over a controlled bandwidth and around the full pipe circumference( max Δt°C= 5/7)
Fast, accurate, reliable and cost-effective
Minimal damage (if any) to factory coating
Equipment is robust and reliable
Simple, lightweight, user-friendly equipment operation
Induction heat is ‘direct into metal’
No deleterious surface residues are produced
No naked flames or exposed elements
Heat is localised and controlled
To ensure that temperature measurements stay within specification use probe temperature
Does away with the need to set aside a large storage area for gas
Unlike gas heating, the induction system is not impaired by very low ambient temperatures
Induction Pre-weld Heating
Pipeline Induction Heat’s pre-weld induction heating systems have been designed for both onshore and offshore field operation, at mainline / front end or double jointing locations. Originally engineered for use on large diameter heavy wall pipes, in association with automatic welding systems, induction pre-heat is equally useful where manual stick-welding is being employed during cold weather conditions.
Re-Heat
In certain circumstances, particularly for offshore fast production pipe lay using automatic welding systems, unexpected delays can disrupt the welding process on the lay barge firing-line.
These ‘hold-ups’ can lead to degradation of the partially welded joint, which may require further filling before it is fully completed. To prevent degradation and embrittlement of the weld, which could lead to a negative NDT / X-ray result down line, VillaMacchine have designed a re-heat induction heating system. This consists of a hinged coil designed to pass heat into the localised area of the weld margin only.
Post Weld Heat Treatment
The post-weld induction heating system is intended for lay barge operation, for diameters ranging from 6″ to 72″, with no limit on wall thickness. Temperature ranges are typically 0 to 650°C.
The purpose of induction post-heating is to provide a rapid, accurate heating cycle, to stress-relieve (anneal) a recently welded pipe joint. This is typically required following specialist automatic welding of very heavy wall pipe, which can result in embrittlement of the weld metal, leading to unacceptable ‘hardness values’. To overcome this problem, the weld area must be subjected to a pre-calculated heat treatment programme, within the fast lay-barge welding production cycle.
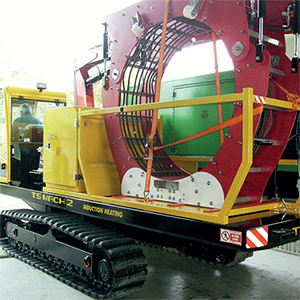
Bevelling Machine
The Villa Macchine’s Pipe Facing Machines are the fastest cutting, most versatile, and user-friendly machines on the market today. Years of experience and the highest quality components are incorporated into every unit.
The machines are powered by a hydraulic circuit as pipe layer.
The PFM machines are designed to machine complex bevel required by automated pipeline welding systems, in addition the machines can be used for:
Producing clean, bright, perfect bevels for manual pipeline welding to maximize quality e minimize repairs
Machining modified bevels on heavy wall pipes to reduce metal volume, therefore reducing welding time
Machining transition tapers or counter bores when joining pipes of different wall thickness
The machines have two major parts, the clamping section and the machining section. The clamp section has two sets of hydraulically powered clamping shoes that are designed to work equally and simultaneously.
The machine is secured to the pipe by expanding the clamp shoes inside the pipe on PFM’s range from 8″ to 90″ pipe. The machining sections of the machine consists of a rotating faceplate with four or six tool holders each holding tungsten carbide cutting tips.
The tools can be set a wide variety of bevel designs and wall thicknesses, Each tool holder may cut a different bevel angle simultaneously .
The PFM operation take from 2 to 6 minutes depending on pipe wall thickness and experience of the operator.
The following documentation will be supply with the machine:
Use and maintenance manual
Spare parts book
CE certification
Test report
Standard Features
High speed beveling
Quick adjustable from 48″ to 60″
Interchangeable clamp section
The machine will be furnished with the clamp section to fit your project
Easily sets up to any bevel configuration
Repetitive, accurate bevels
Brush adapters eliminate both internal and external manual buffing, grinding or sanding
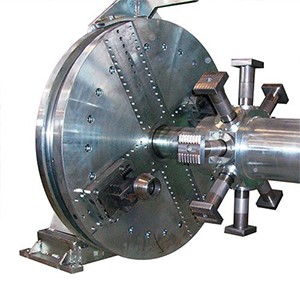
Pneumatic Clamp
The Pneumatic Clamp is used for a correct centering and alignment of pipes.
For the translation, the machine can be provide of axial piston air motor and equipped for manual or automatic welding system.
Its operational cycle is carried out with special pneumatic valves, that in production stage, are controlled manually or at a distance with an appropriate control rod.
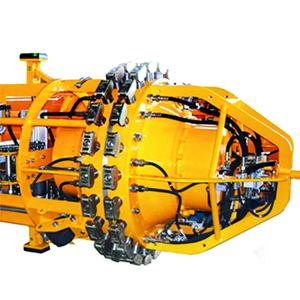